Noticias
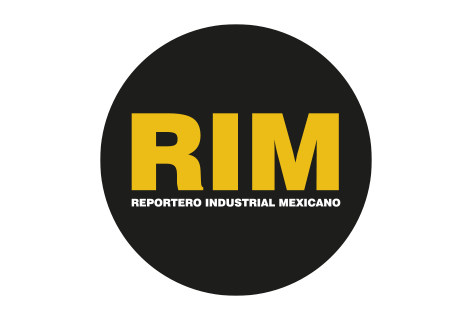
Las herramientas redondas optimizan el maquinado, mejorando productividad y calidad en taladrado, fresado y roscado, con innovaciones como CoroDrill 460 y CoroMill 316 que ofrecen precisión y eficiencia.
En la industria de la metalmecánica, los fabricantes enfrentan el desafío constante de mejorar la productividad y reducir el tiempo de ciclo. Son muchos los elementos en juego, desde máquinas más estables y flexibles, hasta equipos de sujeción con tecnologías que permiten cambios más rápidos y set ups punto cero, así como sistemas de automatización que agilizan la alimentación de las máquinas o celdas de maquinado. En este universo, las herramientas de corte juegan un papel vital, pues nuevas morfologías y materiales que mejoran los avances y la calidad en los procesos de arranque de viruta.
Las herramientas redondas juegan un papel crucial en la consecución de estos objetivos, pues su tecnología ha evolucionado para optimizar los procesos de fabricación. Por ejemplo, en el taladrado, operación fundamental en la metalmecánica, se tiene el reto de asegurar agujeros con tolerancias exactas y superficies acabadas de alta calidad, en busca siempre de ensambles perfectos con una amplia gama de materiales, desde aceros hasta aleaciones no ferrosas, permitiendo a los fabricantes mantener la consistencia en la producción.
Lea también: Los equipos de energía evolucionan a la par de los sistemas OT
Uno de los principales desafíos en el taladrado es la gestión de la evacuación de virutas, que puede afectar la calidad del barreno y, por otro lado, la vida útil de la herramienta. Herramientas como CoroDrill 460, de la firma sueca Sandvik, incorporan geometrías avanzadas y sistemas de refrigeración interna en herramientas que mejoran la evacuación de virutas y permiten operar a mayores velocidades de corte, lo que mejora la productividad de los maquinados.
Herramienta más sujeción
El fresado es otra aplicación crítica donde las herramientas redondas demuestran su valor. En la industria automotriz, por ejemplo, las herramientas de fresado se utilizan para producir componentes de motores y transmisiones con precisiones micrométricas. La capacidad de realizar tanto desbastes pesados como acabados finos con la misma herramienta reduce la necesidad de múltiples configuraciones de máquina, optimizando así el proceso de fabricación.
Uno de los retos clave en el fresado es la necesidad de adaptarse a una variedad de materiales y geometrías de piezas. Las herramientas de corte de carburo sólido ofrecen soluciones versátiles y optimizadas que se pueden personalizar para aplicaciones específicas. En la industria automotriz, durante la fabricación de componentes de motores, la falta de precisión y consistencia en el fresado de ranuras causa productos defectuosos y altos costos de retrabajo.
Nuevas herramientas de fresado son desarrolladas para este tipo de aplicaciones, como el caso de la familia CoroMill 316, que tiene la capacidad hacer cortes con una alta alimentación y con geometrías optimizadas que le permiten mejorar la precisión. A esto se agregan tecnologías como CoroChuck 930 que ofrecen una sujeción más estable, lo que disminuye al máximo desviaciones y el desgaste mismo de las herramientas.
En el maquinado de componentes de titanio, conocidos por su dificultad para maquinarse debido a su alta resistencia y tendencia a generar altas temperaturas durante el corte, como los utilizados en partes de aviones, se las herramientas de corte incorporan carburo sólido que ayudan a reducir las temperaturas de corte y mejorar la evacuación de virutas. Estos avances no solo mejoraron la eficiencia de la producción, sino que también aseguraron la calidad y precisión necesarias para las exigentes aplicaciones aeroespaciales.
Otras operaciones con herramientas redondas, como el roscado y mandrinado automotriz, requieren también de precisión extrema para asegurar la correcta función de las piezas dentro de los mecanismos para los cuales fueron diseñadas. Esto es particularmente importante en la fabricación de componentes de motor y transmisión, donde cualquier desviación puede resultar en fallas de funcionamiento; por lo que contar con herramientas capaces de reducir esfuerzos de corte es clave.
En este sentido, las herramientas deben estar optimizadas para diferentes tipos de materiales y aplicaciones, desde aleaciones de aluminio hasta aceros de alta resistencia, pero garantizando siempre mantener tolerancias estrictas y producir roscas de alta calidad.
Especialistas de Sandvik, aseguran que para enfrentar estos desafíos en los procesos de corte, se tiene que ir más allá de la herramienta y diseñar, por lo tanto, soluciones personalizadas que permiten a los fabricantes adaptar las herramientas a sus necesidades específicas. Esto es especialmente útil en aplicaciones complejas que requieren geometrías de corte únicas o características especiales de la herramienta aunadas integralmente con los sistemas de sujeción y acorde también al tipo de máquina en la cual se lleva a cabo el proceso. En lo general, deben ser trajes hechos a la medida.
Sumado a lo anterior, se identifica el reacondicionamiento de herramientas como otra práctica que ha ganado popularidad entre los fabricantes que buscan maximizar el valor de sus inversiones en herramientas de corte. Estos servicios de reacondicionamiento que restauran las herramientas a su condición original, permitiendo su reutilización y minimizan los costos de adquisición de nuevas herramientas. Este proceso no solo mejora la sustentabilidad al reducir el desperdicio, sino que también asegura que las herramientas mantengan su rendimiento óptimo a lo largo del tiempo.
Las herramientas redondas sólidas son clave para enfrentar los desafíos de productividad y eficiencia en la industria de la metalmecánica. Más allá de la máquina, la sujeción y los periféricos agregados para generar procesos automatizados, las aplicaciones con herramientas de corte, desde el taladrado de alta precisión hasta el fresado eficiente y el roscado automotriz, juegan un importante papel en la manufactura de componentes metálicos.
Otros artículos de interés

Suministro ininterrumpido para la Industria 4.0
La Industria 4.0 representa un salto evolutivo en la manufactura: sistemas físicos,
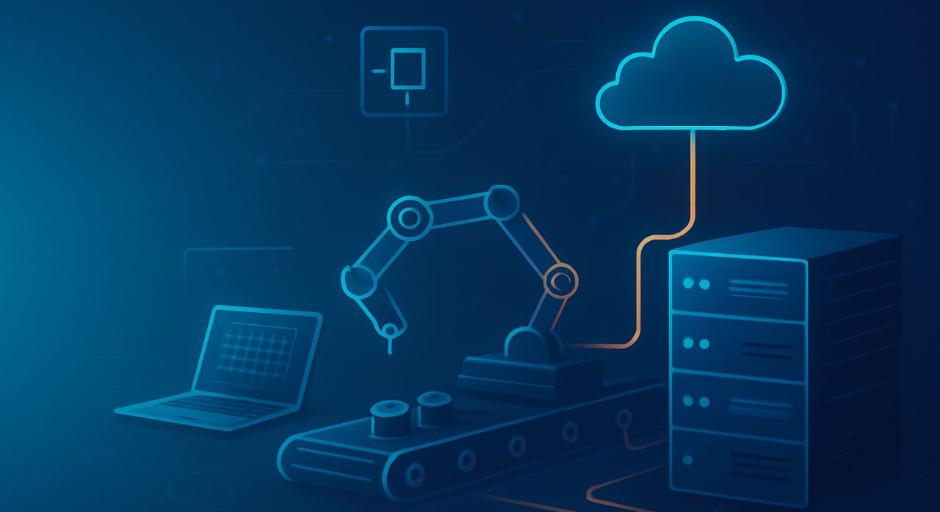
Por qué la manufactura requiere una buena infraestructura de redes
Con la adopción de tecnologías digitales en la manufactura, la infraestructura de

Transporte multimodal gana valor en la industria
En la industria manufacturera mexicana, la logística ha dejado de ser un
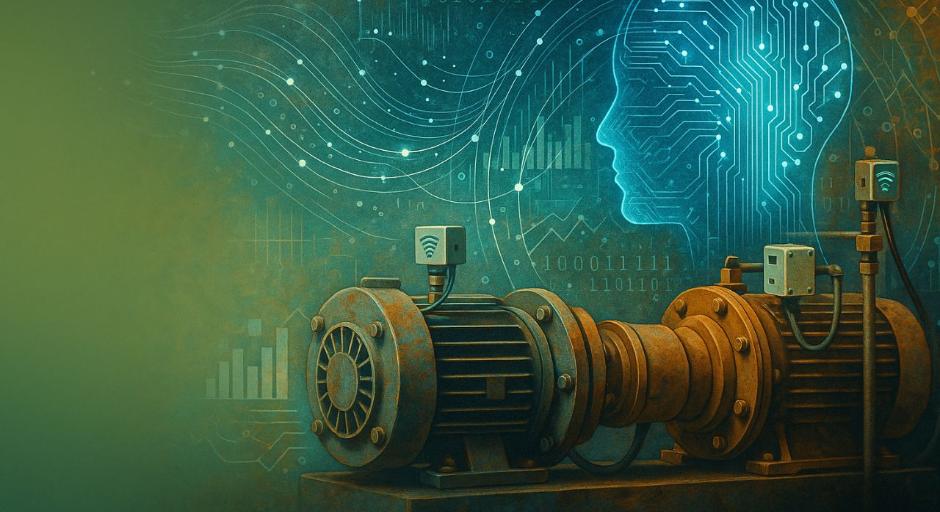
El uso adecuado del IIoT tiene impacto positivo en predictivos
El uso de sensores y sistemas conectados es cada vez más profundo
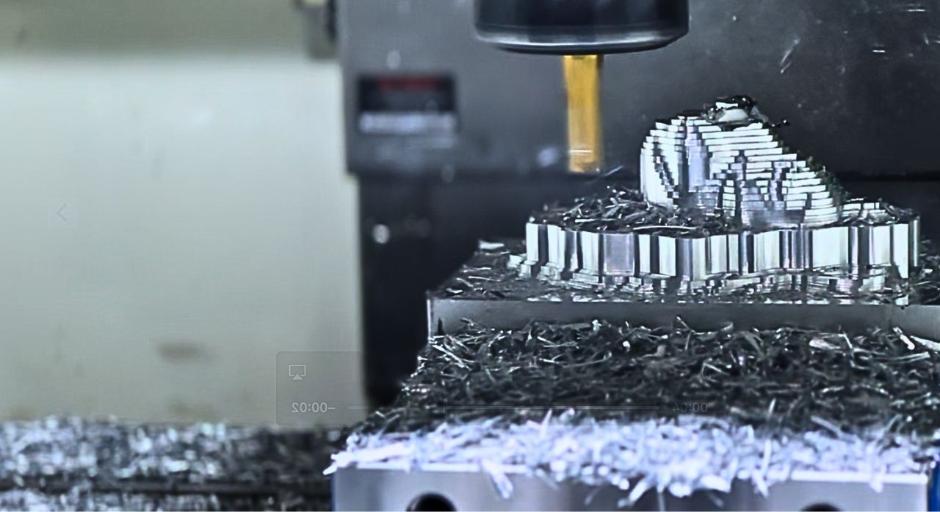
Herramientas de corte: Mayor valor para el maquinado aeroespacial
La industria del maquinado para componentes aeroespaciales en México continúa desarrollándose y

Lubricación: generador de eficiencia en planta
La lubricación influye directamente en la vida útil de maquinaria y en